Heat transfer improvement in fire tubes
Installation of a helix in fire tubes may have a beneficial effect due to
increased mixing. For that reason different configurations of a static and
a moving helix were analysed. In all investigated cases, the external diameter
of the fire tube or the internal diameter of the annular water channel was 50 mm.
The outer diameter of the water channel was set to 90 mm.
D1 | D2 | D3 | D4 | D5 | |
---|---|---|---|---|---|
Helix location | No helix | No helix | Int. partial helix |
Int. full helix |
Ext. rotating helix |
System orientation | Vertical | 45° | 45° | 45° | 45° |
The section under investigation was 1.0 m long. It was preceded by a 0.6 m
long empty channel to allow for flow to develop. Another 0.3 m section was
placed downstream to reduce any effect of outlet boundary conditions.
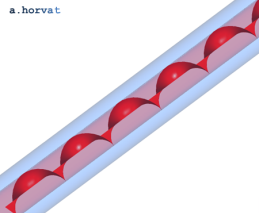
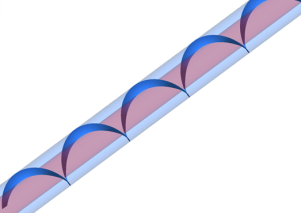
Two of the investigated fire tube configurations: left - internal helix, right - external helix
The parallel flow arrangement was adopted with the inflow of hot gases and the
supply of water being placed at the bottom. A constant water mass flow rate
of 0.425 kg/s was imposed, which for the given arrangement corresponds to the
water velocity of 0.1 m/s. The water inlet temperature was set to 90°C,
which is close to the boiling point.
For the fire tube gas flow, the mass flow rate of 0.0387 kg/s was imposed. It corresponds to the gas velocity of 60 m/s at 800°C. In all cases, the inlet gas temperature was set to 800°C.
For the fire tube gas flow, the mass flow rate of 0.0387 kg/s was imposed. It corresponds to the gas velocity of 60 m/s at 800°C. In all cases, the inlet gas temperature was set to 800°C.
Vapour volume fraction distribution along the fire tube wall - internal helix;
0.0 (blue) ≤ rvap ≤ 0.5 (red) [ ... rotate the graphics with the mouse ]
0.0 (blue) ≤ rvap ≤ 0.5 (red) [ ... rotate the graphics with the mouse ]
The water flow in the annular channel was modelled using the heterogeneous
two-phase model, which allows different velocity and temperature for each phase.
The liquid water phase was modelled as a continuous phase and the steam as
a disperse phase (i.e. a group of bubbles) with an average diameter of 3 mm.
Along the fire tube wall, the water is heated to its saturation point when it starts to boil. To capture the nucleate boiling regime, an additional wall boiling model was implemented. The model accounts for local water superheating, phase change, bubble growth and departure, and subsequent rewetting sequence. All the boiling model parameters are empirically determined for a simple vertical pipe flow [1 & 2] without any boundary layer interference or bubble scrapping effect.
The Ishii-Zuber interphase drag model was used to couple the liquid water and the steam momentum (i.e. velocity fields). The heat transfer between both phases was described using the Ranz-Marshall model. As the buoyancy is an important mixing mechanism on the water side, it was included in the model.
Along the fire tube wall, the water is heated to its saturation point when it starts to boil. To capture the nucleate boiling regime, an additional wall boiling model was implemented. The model accounts for local water superheating, phase change, bubble growth and departure, and subsequent rewetting sequence. All the boiling model parameters are empirically determined for a simple vertical pipe flow [1 & 2] without any boundary layer interference or bubble scrapping effect.
The Ishii-Zuber interphase drag model was used to couple the liquid water and the steam momentum (i.e. velocity fields). The heat transfer between both phases was described using the Ranz-Marshall model. As the buoyancy is an important mixing mechanism on the water side, it was included in the model.
Vapour volume fraction distribution along the fire tube wall - external helix;
0.0 (blue) ≤ rvap ≤ 0.5 (red) [ ... rotate the graphics with the mouse ]
0.0 (blue) ≤ rvap ≤ 0.5 (red) [ ... rotate the graphics with the mouse ]
The conducted analysis showed the extent of heat transfer enhancement due to installation
of a static internal helix in the fire tube. The helix causes periodic interruptions of
the streamwise boundary layer, which significantly improves the near wall mixing.
The external rotating helix sweeps the bubbles from the wall leading to a more uniform distribution of the vapour phase. This delays if not eliminates the boiling crisis, which is in this case characterised by the departure from nucleate boiling (DNB). As a result, much larger heat fluxes are permitted.
The external rotating helix sweeps the bubbles from the wall leading to a more uniform distribution of the vapour phase. This delays if not eliminates the boiling crisis, which is in this case characterised by the departure from nucleate boiling (DNB). As a result, much larger heat fluxes are permitted.
References
- T. Frank, C. Lifante, A.D. Burns, Recent Advances in Modeling and Simulation of Boiling Processes in ANSYS CFD, ANSYS Conference and 27th CADFEM User Meeting, Congress Centre Leipzig, 18-20 November 2009.
- V. Ustinenko, M. Samigulin, A. Ioilev, Tentner, A. Lychagin, A. Razin, V. Girin, Ye. Vanyukov, Validation of CFD-BWR, a New Two-Phase Computational Fluid Dynamics Model for Boiling Water Reactor Analysis, Nucl. Eng. and Design, 2008, Vol. 238, pp. 660–670.
Dr Andrei Horvat
M.Sc. Mechanical Eng.
Ph.D. Nuclear Eng.
phone
+44 79 72 17 27 00
skype
a.horvat
e-mail
mail@caspus.co.uk
M.Sc. Mechanical Eng.
Ph.D. Nuclear Eng.
phone
+44 79 72 17 27 00
skype
a.horvat
mail@caspus.co.uk