Performance assessment of a rotary dryer
In the energy-from-waste power plants the moisture content in the feedstock reduces
thermodynamic efficiency of the conversion process. For that reason, a certain degree of
feedstock drying is necessary. A comprehensive review of the different drying design
concepts was conducted covering batch and continues drying, rotating dryers, fluidized
bed and pneumatic conveying.
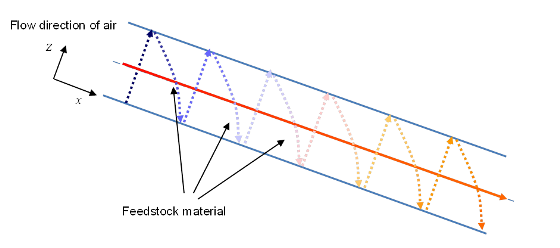
Sketch of the rotary dryer arrangement
An algebraic and a CFD/DEM model of the drying process in the rotary dryer
was developed based on liquid water and water vapour mass balance, feedstock and gas energy balance.
The modelling procedure was successfully validated against the experimental data of Kamke [1].
Such validated modelling procedure allowed us to determine the dryer size parameters and operating conditions
to satisfy the imposed design requirements.
The parametric analysis showed that to reduce the moisture mass fraction for 15%,
the air flow rate of 1.5 m3/s (at the ambient conditions) is required at the elevated
temperature of 160°C. If the preheating is reduced to 80°C, the required air
flow rate increases to 3.4 m3/s. It is worth noting that the required thermal energy
investment in the drying process will be approximately 250 kW although some of this
energy can be later recovered.
An example calculation of the rotory dryer performance is provided below in a form of an embedded script. The main design and operational characteristics of the presented case are identical to those used by Kamke [1]. The dryer operates at the ambient pressure and the environmental temperature of 20°C.
An example calculation of the rotory dryer performance is provided below in a form of an embedded script. The main design and operational characteristics of the presented case are identical to those used by Kamke [1]. The dryer operates at the ambient pressure and the environmental temperature of 20°C.
- Dryer tube diameter:
1.2 m
- Dryer tube length:
5.5 m
- Rotating speed:
5.5 RPM
- Feedstock mass flow rate:
0.294 tonne/hr
- Liquid water vs solid feedstock mass fraction @ inlet:
1.352
- Feedstock temperature @ inlet:
24.1°C
- Representative particle diameter:
2.06 mm
- Mass flow rate of gas @ inlet:
kg/s
- Gas temperature @ inlet:
°C
Mass flow evaporated liquid water from the feedstock:
Total power required for the drying process:
Energy per mass of feedstock @ inlet:
Total power required for the drying process:
Energy per mass of feedstock @ inlet:
References
- F.A. Kamke, J.B. Wilson, Computer Simulation of a Rotary Dryer - Part II: Heat and Mass Transfer, AlChE Journal, Vol. 32, No. 2, February, 1986, pp. 268-275.
Dr Andrei Horvat
M.Sc. Mechanical Eng.
Ph.D. Nuclear Eng.
phone
+44 79 72 17 27 00
skype
a.horvat
e-mail
mail@caspus.co.uk
M.Sc. Mechanical Eng.
Ph.D. Nuclear Eng.
phone
+44 79 72 17 27 00
skype
a.horvat
mail@caspus.co.uk