Many components of ITER Neutral Beam (NB) will be subjected to significant heat loads,
and therefore require active water cooling during their operation. The cooling network
that is an integral part of exposed structural elements will be manufactured using
the deep-hole drilling (DHD) technique.
In a maintenance scenario, these components will be removed and transported to
a maintenance facility. ITER requires that in such a scenario there is no liquid
water left anywhere inside the internal cooling circuitry as it may contain tritium.
Although most of the components will be drained by gravity, the NB duct liner cooling panels will require fast blow-out
using nitrogen gas. Such purging procedure shall remove most of the water and leave all passages clear.
At the end, dry heated nitrogen gas will be circulated through the same coolant circuits
to evaporate the remaining water.
Draining of ITER NBDI duct liner side panels by blow-out
Cooling network example with parallel flow paths during a blow-out sequence:
red - hot liquid coolant and blue - cold nitrogen gas
red - hot liquid coolant and blue - cold nitrogen gas

The main problem with the force blow-out arises in circuits with parallel flow paths. In such arrangements,
it is possible that the adequate pressure required for purging cannot be sustained for all parts of the cooling circuit.
This is especially problematic for vertical arrangements will a large hydrostatic head and poorly balanced
coolant networks.
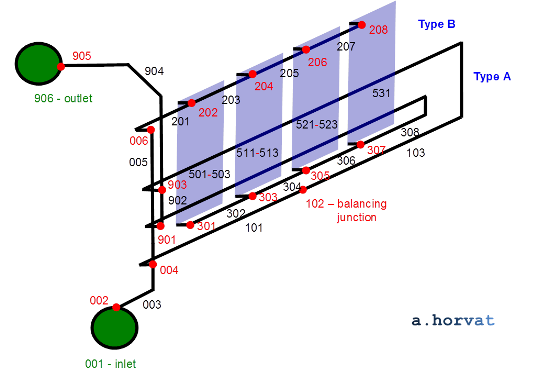
Cooling network model of ITER NB duct liner side panels [1]
A number of analysis projects had been conducted for the ITER NB duct liner, fast shutter and exit scraper to
balance their cooling network and to demonstrate success of the blow-out sequence using the available nitrogen pressure supply.
The required two-phase flow transient simulations were performed using WAHA [2] or RELAP5 Mod 3.3 code.
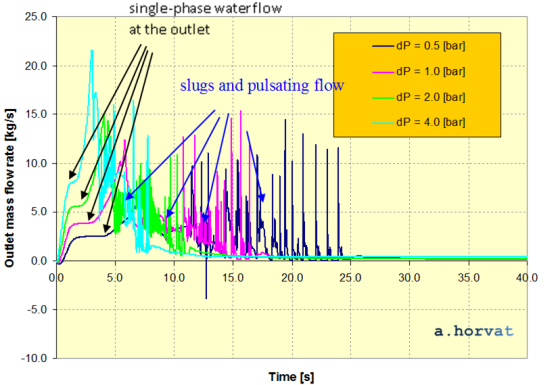
Outlet mass flow rate from ITER NB side panels - flow regime identification [1]
References
- S. Mistry, A. Horvat, R. Verhoeven, Y. Xue, Thermo-Hydraulic Design of the ITER HNB Duct Liner Modules, Fusion Engineering and Design, 2013, Vol. 88, pp. 930-934.
- J. Gale, I. Tiselj, I. Parzer, A. Horvat, Two-Fluid Model of the WAHA Code for Simulation of Water Hammer Transients, Multiphase Science and Technology, 2008, Vol. 20. Issue 3-4, pp. 291-322.
Dr Andrei Horvat
M.Sc. Mechanical Eng.
Ph.D. Nuclear Eng.
phone
+44 79 72 17 27 00
skype
a.horvat
e-mail
mail@caspus.co.uk
M.Sc. Mechanical Eng.
Ph.D. Nuclear Eng.
phone
+44 79 72 17 27 00
skype
a.horvat
mail@caspus.co.uk